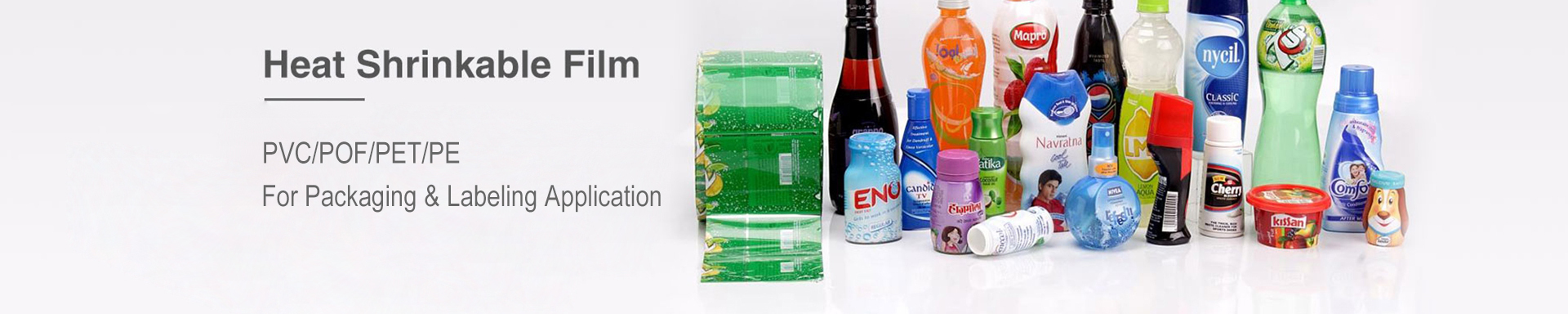
Are some production processes of PVC shrink film complicated?
2024-02-23 16:19Heat shrinkable film has the characteristics of cleanliness, environmental protection, high transparency, high shrinkage, good heat sealing performance, high surface gloss, good toughness, high tear strength, uniform thermal shrinkage and suitability for automatic packaging, etc. It is the replacement product of the old-fashioned PVC heat shrinkable film. At present, POFC-3 is widely used in the outer packaging of food, beverage, alcohol, electrical products, electronic products, toys, daily necessities and other products.
Lightweight packaging in heat shrinkable film should become the mainstream trend. Lightweight packaging is beneficial to the environment and the profits of enterprises. Lightweight is a commonly used industrial term at present, which is used to describe the practice of reducing the weight of packaging by using less materials.
At present, the application of heat shrinkable film in the domestic market mainly shows the following characteristics:
1. It is of great significance to apply the combination of heat-shrinkable film and gas-phase antirust technology to replace antirust oil in hardware tools to enhance antirust ability;
2. It has been widely used in fast food, ceramic products, tea sets, mechanical parts and other areas;
3. It can be used for labels of various bottled beer and beverages, which can reduce the process of removing labels and facilitate recycling;
4, used for bottled beer instead of tying rope packaging to prevent bottled beer from hurting people;
5. Heat shrinkable film is also the patron saint of building and transportation materials. It is not only suitable for the packaging of multiple products and packaging with pallets, but also convenient for transportation and sales, easy to realize mechanization and save labor and material resources, and can partially replace the packaging of cartons and wooden cases;
Some production processes of PVC shrink film are not complicated. Ordinary production lines are generally composed of a roller, a printing machine, a back coating machine and a cutting machine. The film with a thickness of only 0.3mm to 0.7mm is produced mainly through the direct stirring of the roller, the rotation of the roller and high-temperature rolling. At the same time of production, colors are printed on the front of the film by the printing machine, and a layer of back coating is attached to the back of the film by the back coating machine.
Don't underestimate this back coating, it is an important determination of PVC film performance. The back coating is made of special materials and is an affinity agent. It is precisely because of this back coating that the pvc film can be tightly integrated with the medium density board or other boards, and it will not be opened for ten or even fifteen years.
However, the problem of ordinary film sticking is that it can't solve the problem of film falling off. Because the whole production process is carried out at high temperature (the temperature in the roller reaches 220 degrees), PVC film has high light resistance and fire resistance.
Of course, this requires a lot of production machines. Usually, the production equipment cost of a production line is about 39 million marks, equivalent to about 160 million yuan. On the other hand, the production process of PVC shrink film is quite simple, and the machine output is also very large, so PVC shrink film is actually a low-input and high-yield product.
Heat shrinkable film can be obtained by stretching and cooling the PVC film after preheating (as long as it is not heat-set). At Tf close to PVC resin, the resin casting was stretched horizontally and vertically, and then quenched, so that the resin molecular chain was frozen in the oriented state, and heat shrinkable film was formed. The process from raw materials to heat shrinkable film is a process of entropy reduction, and the thermodynamic state of heat shrinkable film is unstable. When the shrink film is subjected to heat treatment, the oriented molecular chain will slowly return to random coil (curled state), and the film will shrink. However, the effects of longitudinal shrinkage and transverse shrinkage of the film are different. If the longitudinal shrinkage is too large, the PVC film will wrinkle. Only the film with large transverse shrinkage and small longitudinal shrinkage can keep smooth and wrinkle-free.
Different container shapes have different requirements for shrinkage of materials. For example, OPP or PVC materials can be considered for approximate cylindrical containers with low shrinkage requirements, while OPS films with high shrinkage and strength can be considered for containers with multi-curve or streamlined design. OPS film can be closely attached to containers with different shapes, which can not only print exquisite patterns, but also achieve the use of novel packaging containers with different shapes. OPS is clean and odorless, and it is not afraid of grease, which conforms to food hygiene standards. It allows designers to adopt eye-catching colors, realize 360 label design, and give full play to creativity and imagination, thus making label patterns more vivid, highlighting the image on the shelf and producing unexpected container effects. For example, the curve glass bottle newly promoted by Blue Ribbon Beer in China adopts high shrinkage OPS substrate and uses solvent-based adhesive for labeling.